What Is The Best Solution for Welding Galvanized Steels?
Let’s get straight to the point. We know that welding galvanized steels is problematic because the galvanize burns off during welding, with zinc vaporizing at high temperatures and zinc oxides accumulating in the weld. Not only do we lose the corrosion-resistant properties of the galvanizing, but the weld is also likely to contain multiple defects.
The number one solution preferred for welding galvanized steels in high-precision manufacturing, especially in industries like automotive, is using copper-silicon alloy filler materials. While there are other alternatives (such as ER70S-2 or some special FCWs), since this article focuses on the "best solution," I won't mention additional options here.
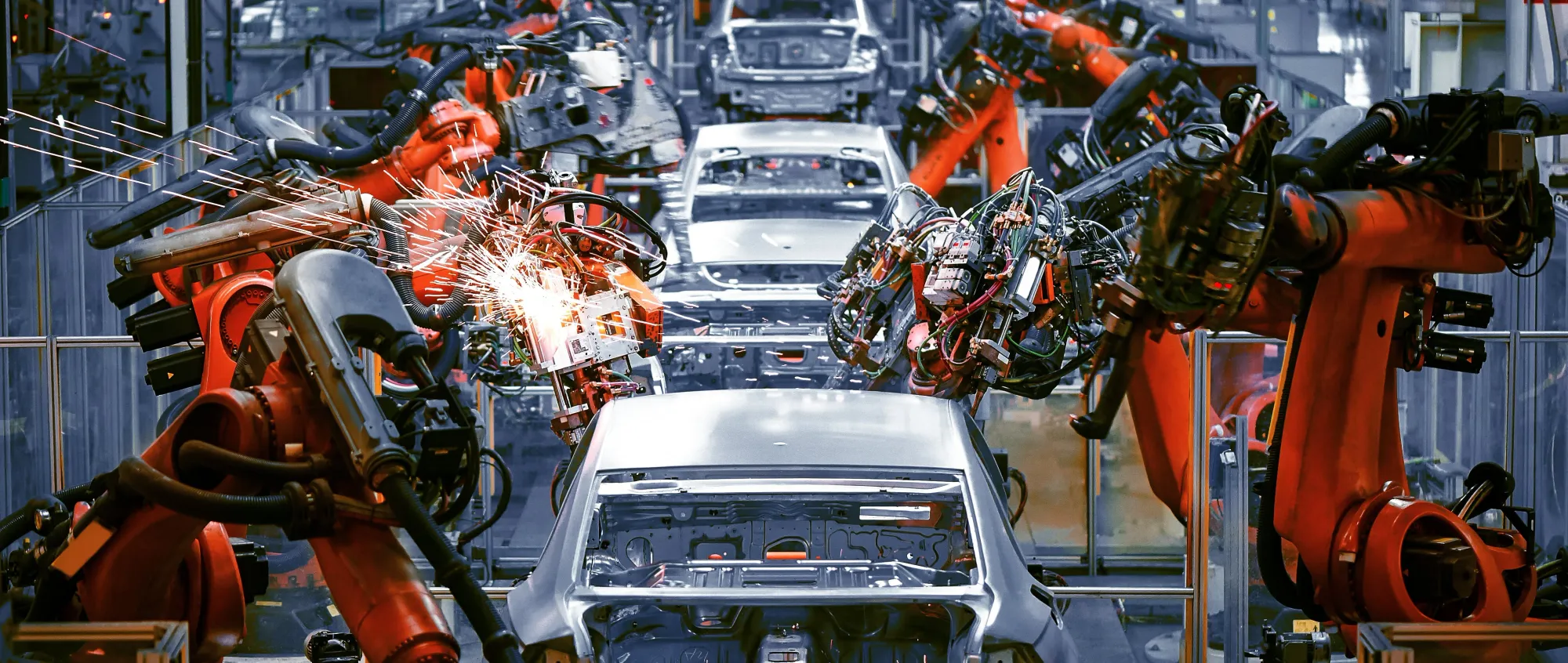
For gas metal arc welding of galvanized steels, the products compliant with the AWS/ASME SFA - 5.7 ERCuSi-A standard are considered the best alternative for several key reasons:
Copper-Silicon Alloy: ERCuSi-A welding wire is composed of a copper and silicon alloy. This alloy helps prevent zinc from vaporizing at high temperatures and reduces the accumulation of zinc oxides during welding, resulting in a smoother and cleaner weld pool when welding galvanized steels. This improves weld quality and reduces the need for post-weld treatments.
Reduced Zinc Vaporization: The zinc coating on galvanized steel surfaces vaporizes quickly at high temperatures, which can cause issues during welding. ERCuSi-A welding wire minimizes the effects of vaporized zinc, reducing the formation of porosity and cracks during welding. This ensures a stronger and more durable weld.
Excellent Corrosion Resistance: Copper-silicon alloy wires create a weld seam that is compatible with the zinc coating of galvanized steel. This makes the welded area resistant to corrosion, maintaining the original galvanized protection of the steel after welding.
Good Mechanical Properties: Welds made with wires that meet ERCuSi-A standards provide good mechanical properties such as high strength, impact resistance, and flexibility. These features enhance the durability of the welds, ensuring reliable welding performance in galvanized steel structures.
Low Spatter and Clean Welds: Using this type of wire results in low spatter and a cleaner weld surface, which reduces labor costs and minimizes the need for post-weld cleaning or grinding.
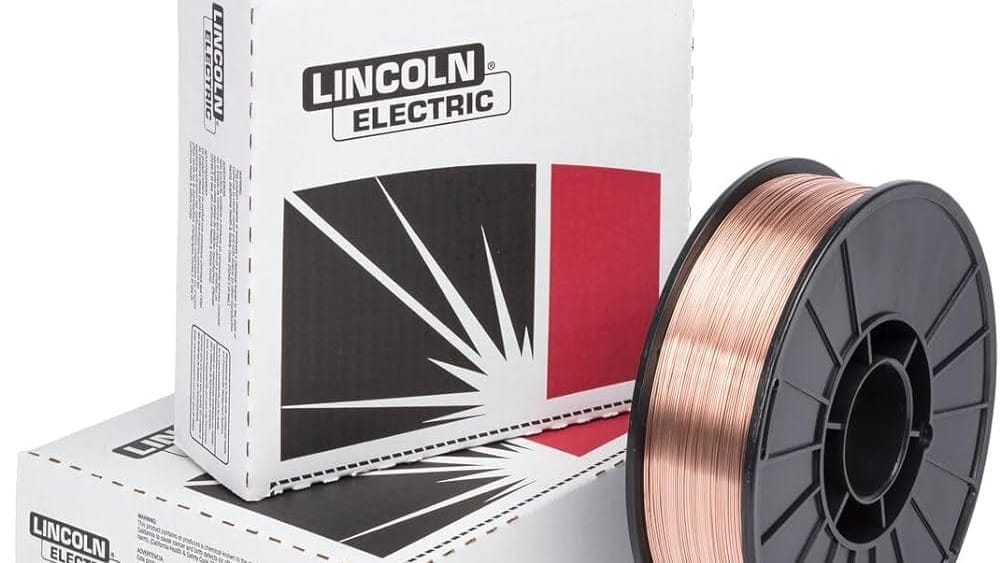
In summary, welding wires that meet the AWS/ASME SFA - 5.7 ERCuSi-A standard are one of the best alternatives for welding galvanized steels because they provide high-quality, corrosion-resistant, clean, and mechanically strong welds.
I'll show you a few example products from global brands, so you can review them and gain a broader understanding as well.
- ESAB - OK Autrod 19.30
- Lincoln Electric - SuperGlaze SiBR
- voestalpine Böhler Welding - UTP A 384
Discussion