Welding Defects and the Role of Sound Analysis
Welding is a complex process where even the most well-prepared setup can have unexpected consequences. Factors like contamination, bevel misalignment, or improper shielding gas can all lead to defects that compromise weld quality. This is where recent advancements in sound and imaging technology come into play, offering a new way to detect these issues in real time.
The concept revolves around analyzing the sound produced during welding. A proper weld has a distinct audio signature, and any deviation can indicate a potential problem. Here I discover a specially designed microphone from Xiris that can be integrated into their cameras.
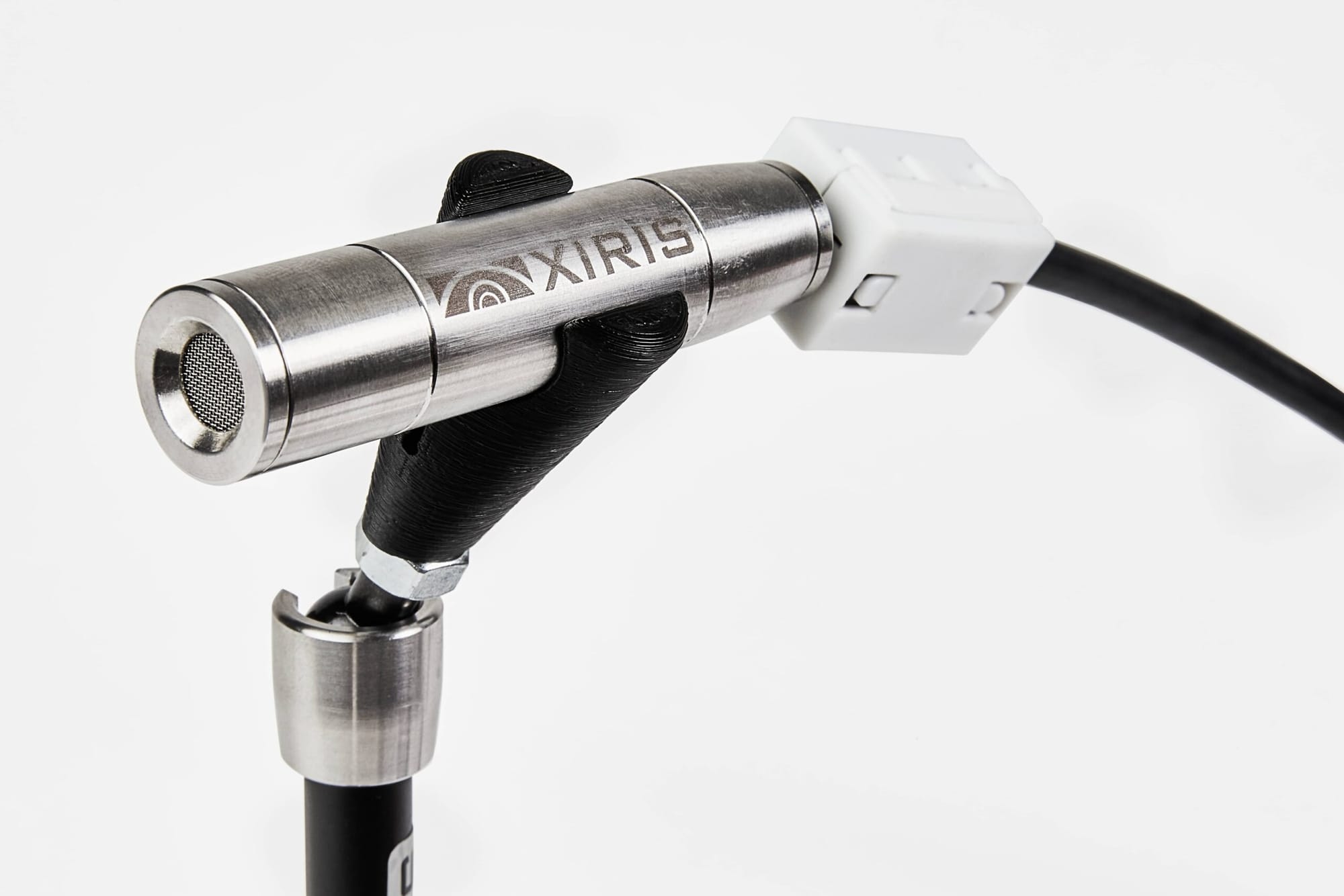
With tools that capture and analyze welding sounds right at the source, operators can be alerted immediately if something goes wrong. This technology not only helps detect issues like porosity or burn-through but also aids in reducing the reliance on manual inspection, making the welding process more consistent and reliable.
Using artificial intelligence, these systems can learn what a good weld should sound like and flag anomalies during production. This means that welders can focus more on optimizing processes rather than manually checking for defects. As welding moves towards greater automation, integrating sound analysis with imaging offers a promising way to enhance both quality and productivity.
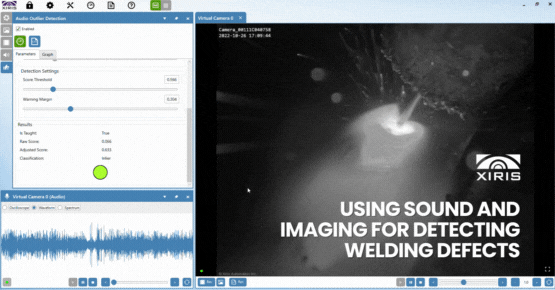
Discussion