Ultrasonic MIG Welding Improves Aluminum Alloy Performance
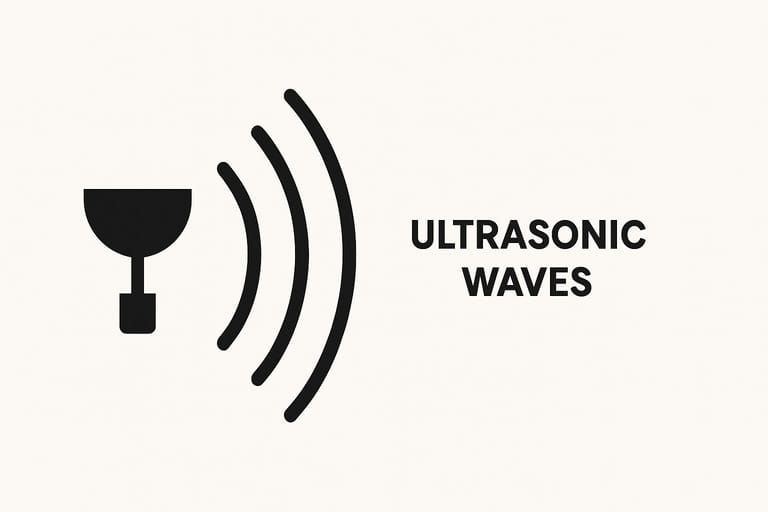
Recent research explored how high-energy ultrasonic waves can reduce welding deformation and enhance joint performance in LC52 aluminum alloy plates. By injecting ultrasonic energy during MIG welding, the study reported an average 65% or greater drop in welding residual stress, with stress becoming more uniformly distributed.
The process, referred to as “low stress welding,” effectively decreased overall plate deformation by nearly 69%. Metallographic examinations also revealed that high-energy ultrasound refined grain structures in the weld zone, fusion zone, and heat-affected zone, reducing defects like pores and cracks.
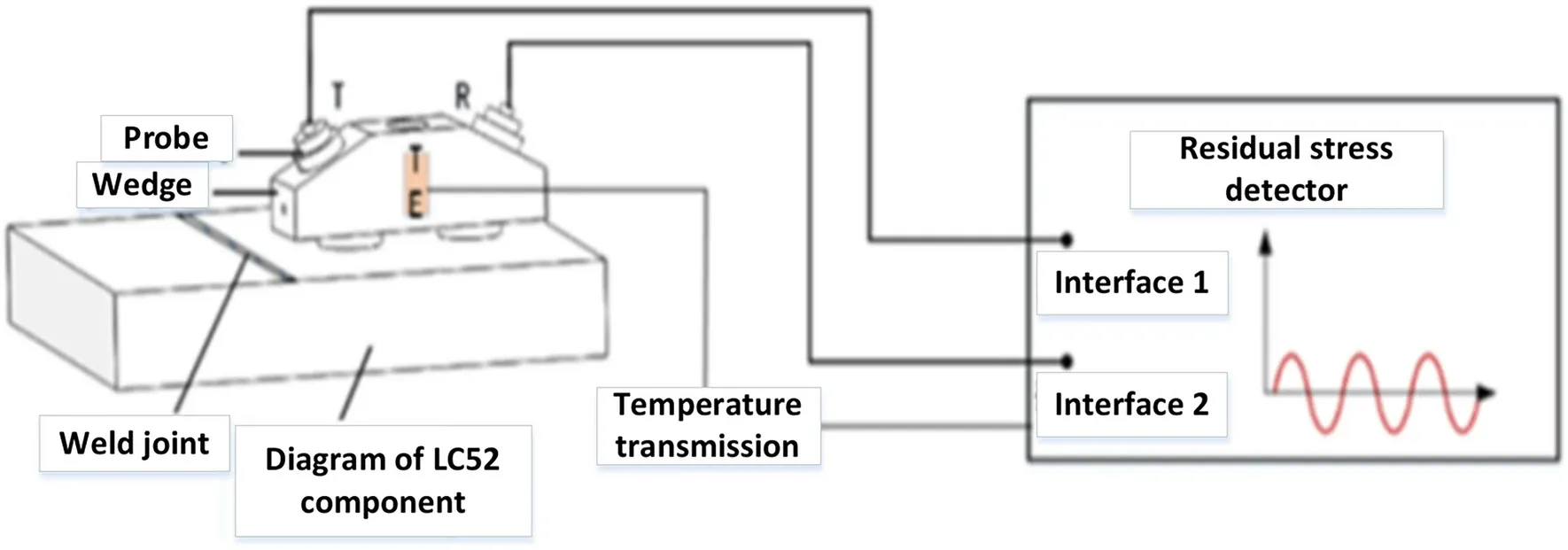
The mechanical tests backed these findings: tensile strength of the ultrasonically assisted welds rose by about 24%, and impact resistance in the fusion and heat-affected zones improved substantially. Fracture analysis indicated fewer and smaller micro pore defects, suggesting stronger, more reliable welds overall.
This approach points to a promising avenue for welding LC52 and other aluminum alloys where reduced residual stress and enhanced toughness are critical. Researchers believe it could benefit industries from aerospace to automotive, where the integrity and durability of welded components are paramount.
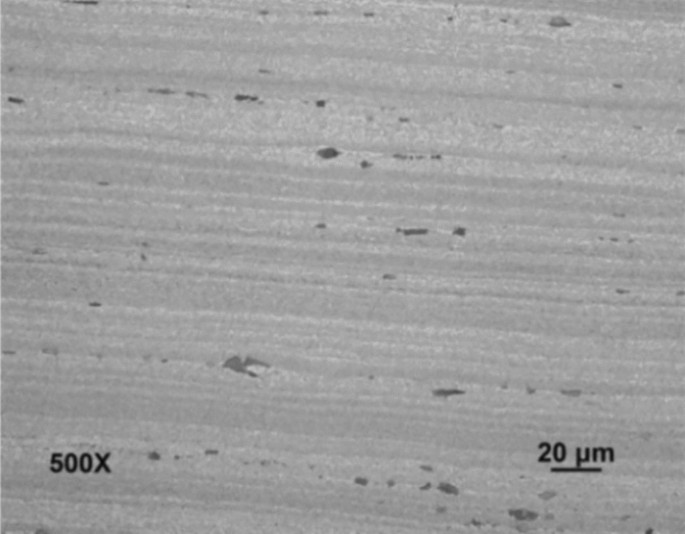
Discussion