Top 5 Essential Tips for Titanium Welding
Titanium is widely used in industries like chemical, petrochemical, maritime, oil and gas, energy, and pharmaceuticals for piping and tanks. Its corrosion resistance, high strength-to-weight ratio, and durability under extreme temperatures make it ideal for handling corrosive materials.
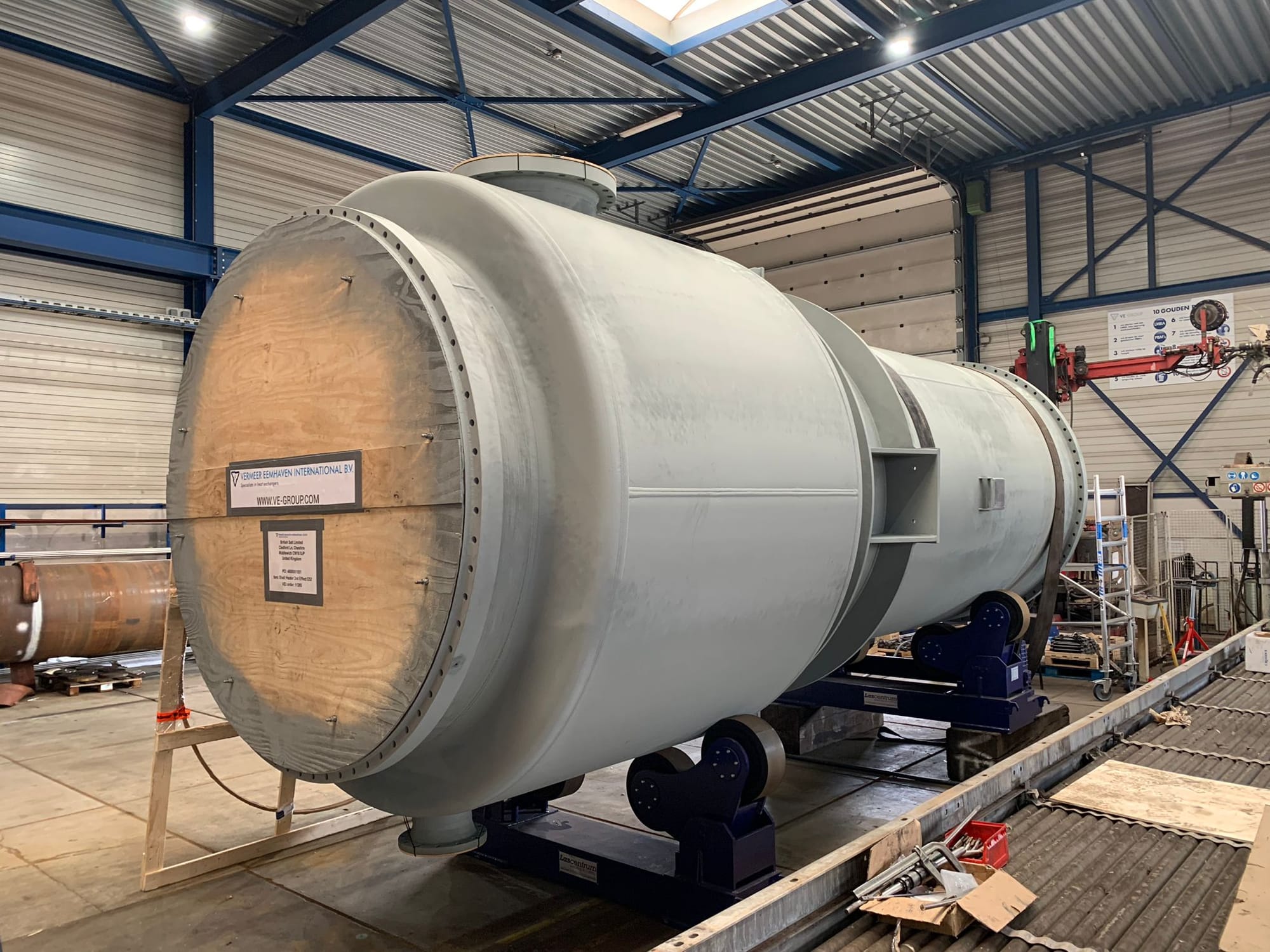
Titanium welding presents unique challenges due to the material's high reactivity at elevated temperatures. To achieve high-quality welds, welding engineers must adhere to specific practices that prevent contamination and ensure structural integrity. Based on industry experiences and technical insights, here are the top five essential tips for titanium welding:
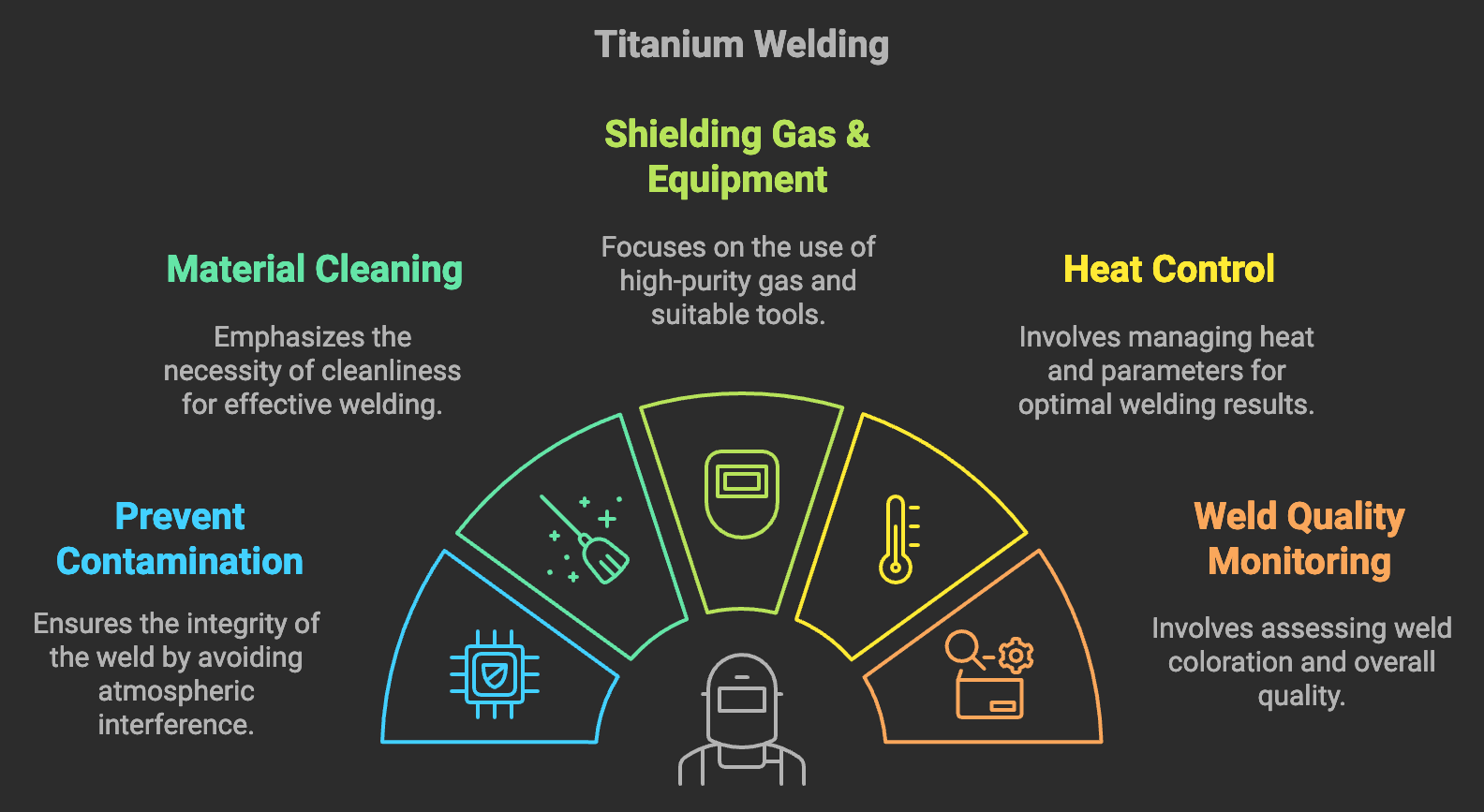
1. Prevent Atmospheric Contamination
Critical Temperatures: Titanium becomes highly reactive with hydrogen, oxygen, and nitrogen between 800°C and 400°C during cooling. This reactivity leads to the formation of brittle compounds that can compromise weld integrity.
Protective Measures:
- Shielding Gas Coverage: Ensure the weld pool is adequately shielded from the atmosphere using high-purity inert gases.
- Use of Trailing Shields: Implement trailing shields or gas cups that extend gas coverage over the weld pool and heat-affected zone during welding and cooling.
- Extended Post-Gas Flow: Maintain shielding gas flow for at least 15 seconds after welding to protect the cooling weld from atmospheric gases.
2. Thorough Cleaning of Materials and Consumables
Importance of Cleanliness: Contaminants such as oils, dirt, and residues introduce hydrogen and other impurities into the weld, leading to defects and embrittlement.
Cleaning Protocols:
- Base Material Preparation: Mechanically clean the weld area using stainless steel brushes or abrasive tools dedicated to titanium to avoid cross-contamination.
- Filler Wire Handling: Clean filler wires with acetone and handle them with clean gloves. Do not lay wires on contaminated surfaces.
- Tooling: Use grinding wheels and abrasives exclusively reserved for titanium to prevent the introduction of foreign materials.

3. Utilize High-Purity Shielding Gas and Proper Equipment
Gas Selection:
- High-Purity Argon: Use 99.999% pure argon gas to minimize the presence of reactive gases like oxygen and nitrogen.
- Flow Rates: Adjust gas flow rates according to nozzle size, typically higher than standard welding to ensure adequate coverage.
Equipment Considerations:
- Gas Lens and Nozzles: Employ large-diameter gas lenses and cups to provide a laminar gas flow that envelops the weld area.
- Backup Shielding: For root-side protection, use purge dams or backing bars to introduce shielding gas to the underside of the weld.
4. Control Heat Input and Welding Parameters
Heat Management: Excessive heat increases the risk of oxidation and contamination.
Welding Techniques:
- Amperage Control: Use the lowest amperage necessary to achieve proper fusion. Avoid exceeding 150-160 Amps for most applications.
- Pulse Welding: Implement pulsed TIG welding to reduce heat input and allow the weld to cool between pulses.
- Travel Speed: Maintain a consistent and appropriate travel speed to prevent overheating and ensure uniform bead appearance.
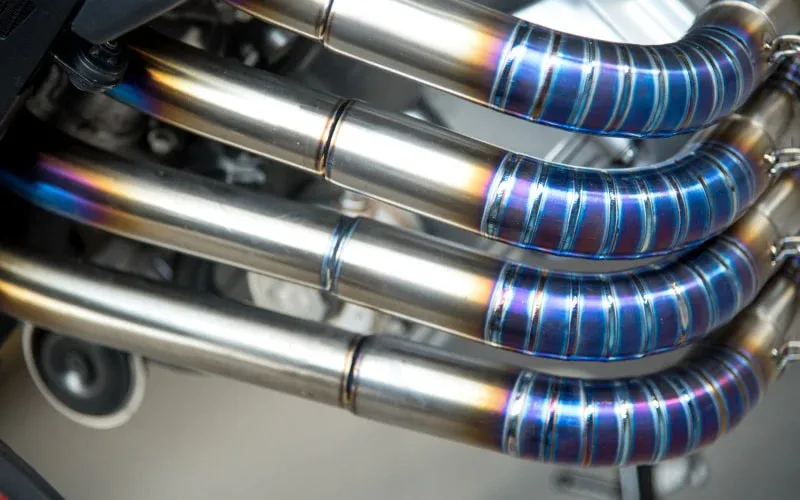
5. Monitor Weld Coloration and Quality
Color Indicators: The color of the weld bead is a visual indicator of contamination levels.
Acceptable Colors:
- Silver to Light Straw: Indicates minimal oxidation and acceptable weld quality.
Unacceptable Colors:
- Blue, Purple, Red Hues: Signify excessive contamination by atmospheric gases leading to embrittlement.
Quality Assurance:
- Visual Inspection: Regularly inspect welds for color changes and surface defects.
- Rework Protocols: If unacceptable coloration is observed, remove the affected weld area and re-weld under proper shielding conditions.
Discussion