The Truth Behind GMAW Welding Wires: ER70S-6 or ER70S-3?
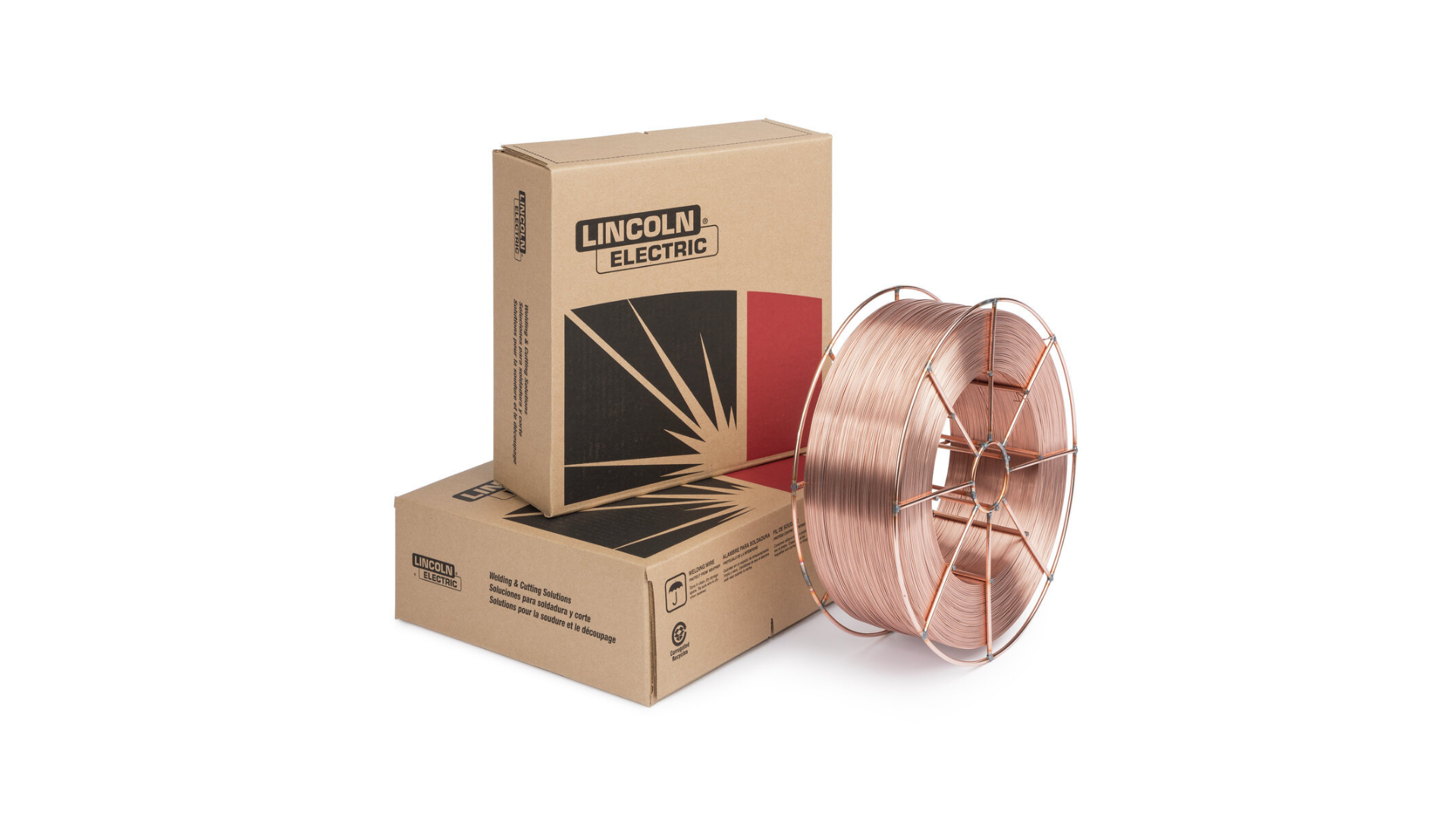
The welding industry has long been influenced by marketing strategies that sometimes outshine technical expertise, and senior welding engineer Emily Craig isn’t afraid to call it out. In a thought-provoking LinkedIn post from last week, Craig laid bare the history of how GMA welding wire preferences shifted—and not always for the better.
In the early days, two distinct carbon steel weld wires dominated the gas metal arc welding (GMAW) scene: E70S-3 (aka 2Si) and E70S-6 (aka 3Si1 or 4Si1). As Craig explains, E70S-6, with its high silicon and manganese content, was initially developed to combat porosity when welding with reactive CO2 gas. Meanwhile, E70S-3 was optimized for use with less reactive argon-rich gas mixtures, producing cleaner welds with minimal slag. Despite its specific role, E70S-6 was marketed as a premium wire due to its higher cost, often misleading users into believing it was universally superior.
By the 1980s, as argon-based gas mixes gained popularity, North American weld wire manufacturers capitalized on the situation. To protect their market share, they promoted E70S-6 wires as a premium product, even for applications where E70S-3 would have sufficed. This led industries, starting with automotive and truck manufacturing, to adopt E70S-6 wires universally. Ironically, as Craig points out, this choice often resulted in undesirable slag islands (aka. Si island) that compromised paint and coating quality.
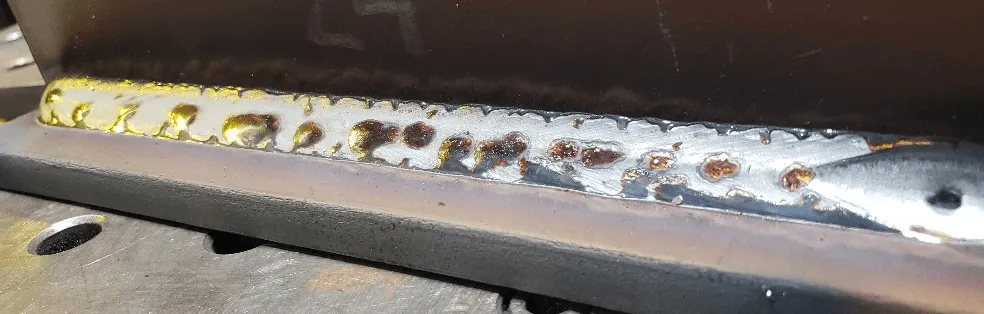
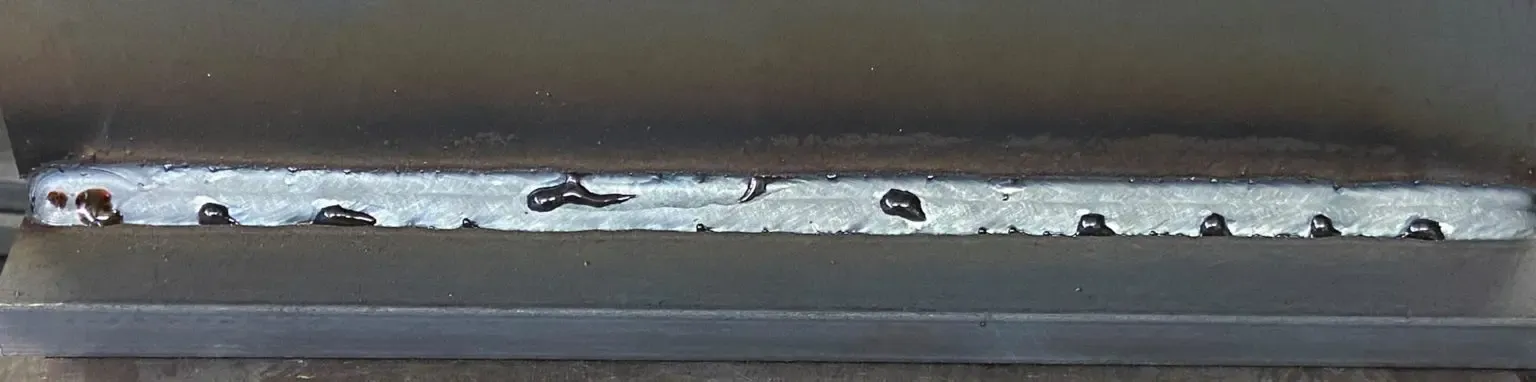
Craig’s insights reveal how a lack of technical understanding among engineers and supervisors allowed marketing narratives to dominate decision-making. Instead of choosing the most suitable wire, many industries defaulted to the costlier option, assuming it was better. Craig advocates for a return to basics: demanding simpler gas mixes and the appropriately priced E70S-3 wire for argon-based applications. As she aptly puts it, the industry must stop prioritizing sales-driven advice over sound technical expertise.
Craig's words serve as a wake-up call to welding professionals. If shops and engineers focus on understanding the technical requirements of their work instead of following marketing trends, they can achieve better weld quality and cost efficiency. Emily Craig’s message is clear: the welding industry needs to value expertise over hype.
Lastly, I’d like to point out a technical detail that might seem minor to some but is worth mentioning. You can see that there’s no difference in the stress test requirements for the relevant standard notations. In terms of chemical properties, it’s also clear which maximum or minimum values are specified for Mn-Si content. This factor impacts the impact testing of welded parts (table.3), as ER70S-3 achieves 27J at -20°C, while the same value is achieved with ER70S-6 wires at -30°C.
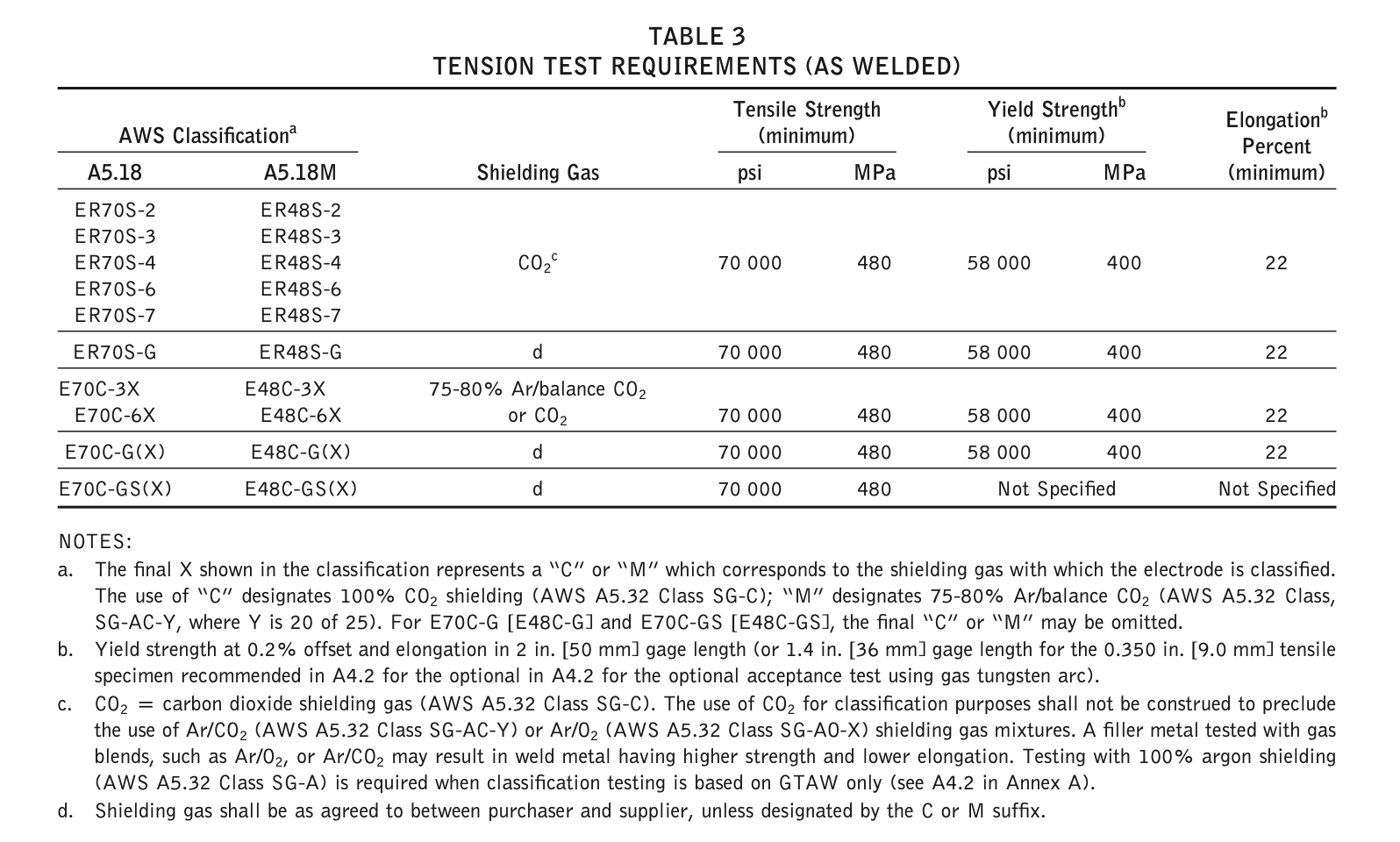
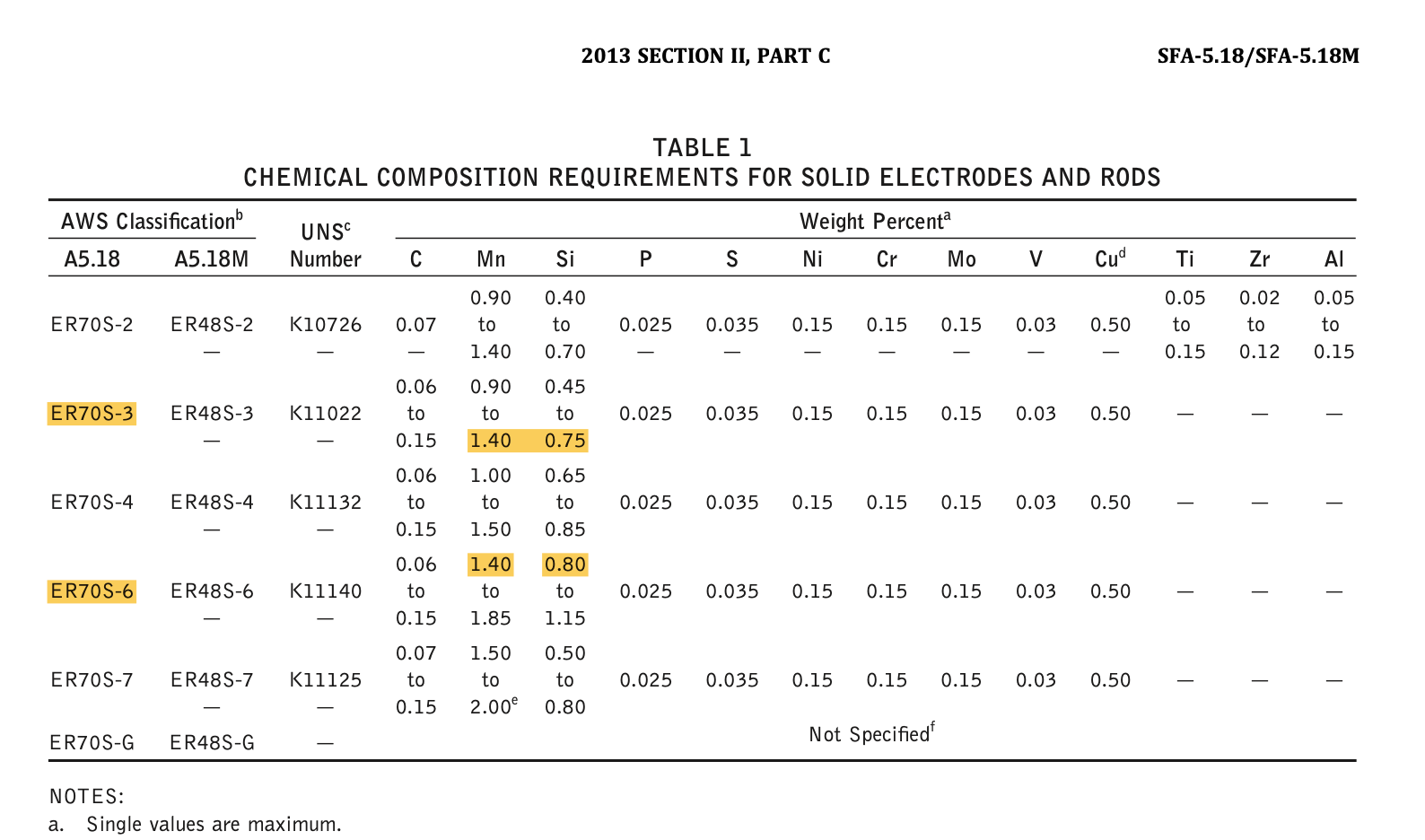
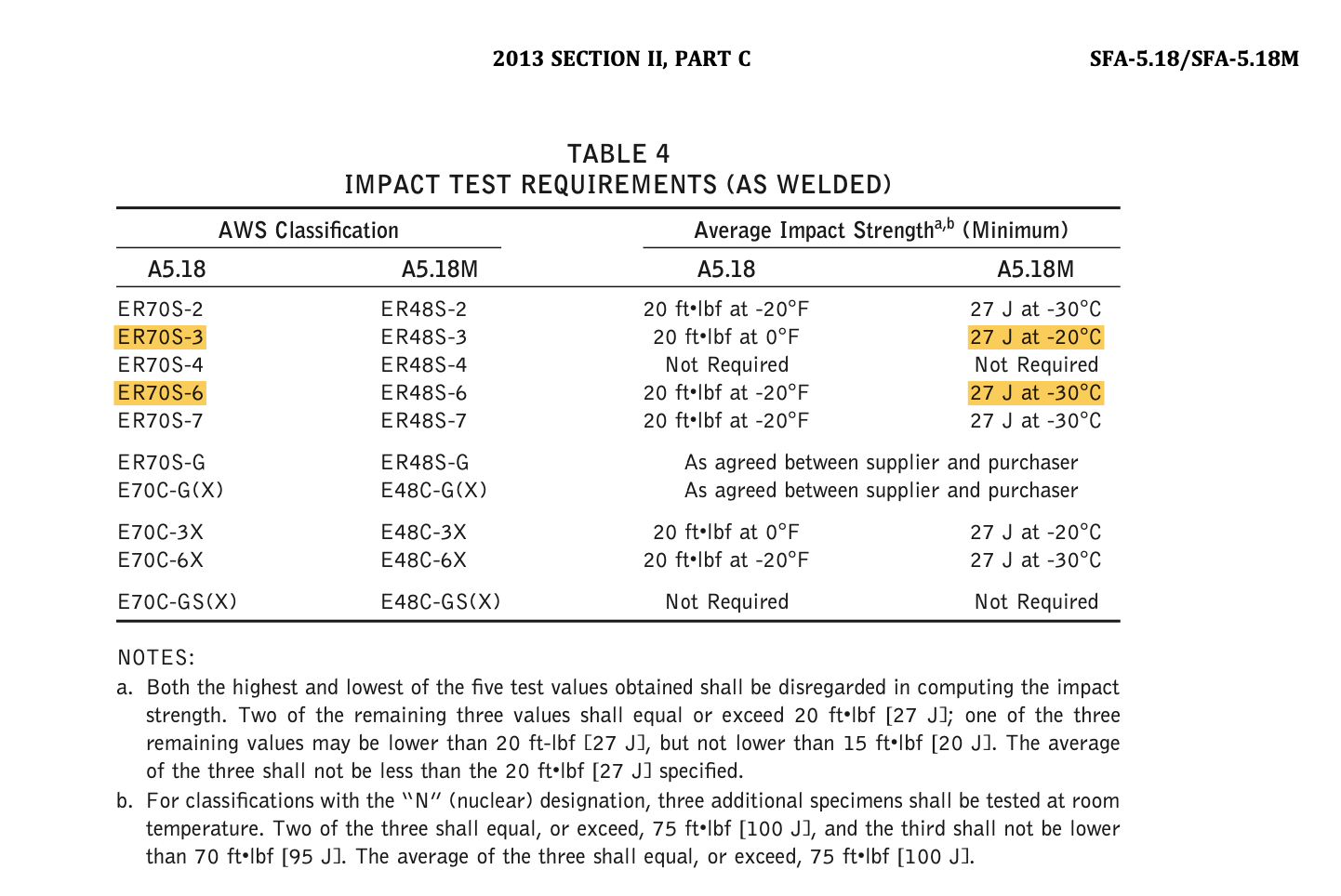
Discussion