Rotary Friction Welding Revolutionizes Power Station Repairs
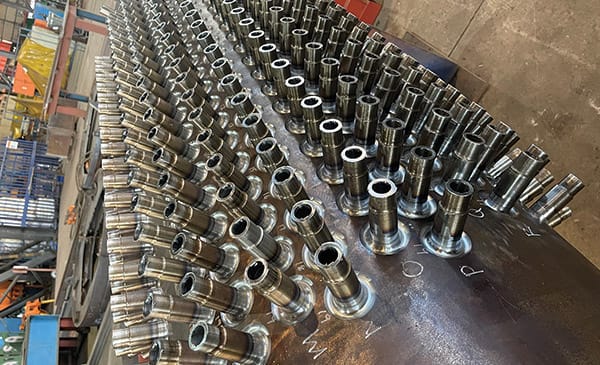
Steinmüller Africa, one of the leading companies in the production of high-pressure steam, together with eNtsa, an engineering consultancy, proved this with a groundbreaking application of rotary friction welding before 2024. This approach successfully repaired four high-pressure water heater boiler headers at the Tutuka power station in Mpumalanga, achieving results that were 100% defect-free.
The project involved attaching 448 heat exchanger nozzles to each header using a hybrid of rotary friction welding and friction hydro-pillar processing (FHPP). Originally, submerged arc welding was used, but defects in the initial headers required a new approach. By developing and implementing this novel welding technique, the companies resolved the issues while achieving remarkable benefits: 75% faster welding times, minimal distortion, and no increase in manufacturing costs.
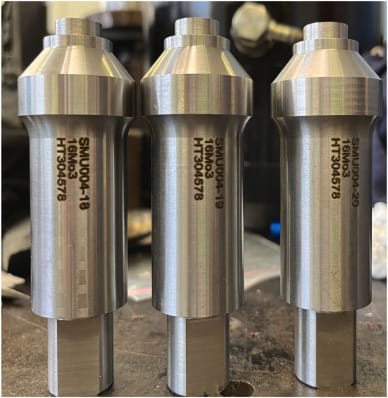
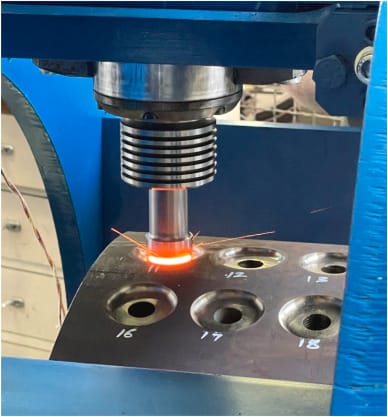
At the core of this innovation was WeldCore technology, a repair and sampling method that enabled precise, reliable, and compliant welds. This method ensures long-term reliability, reducing the risks of catastrophic failures while boosting uptime—a critical factor in the power generation industry.
This welding process holds promise for industries beyond power generation, including petrochemical and nuclear sectors, where strong, defect-free nozzle-to-pipe connections are essential. By collaborating to refine and approve this technique, Steinmüller Africa and eNtsa have not only solved a pressing challenge but also set a precedent for how advanced welding technologies can redefine industry standards.
Finally, readers can access the article published in ScienceDirect via this link.
Discussion