New Welding Wire Introduced: UTP ROBOTIC CHROMELESS 600
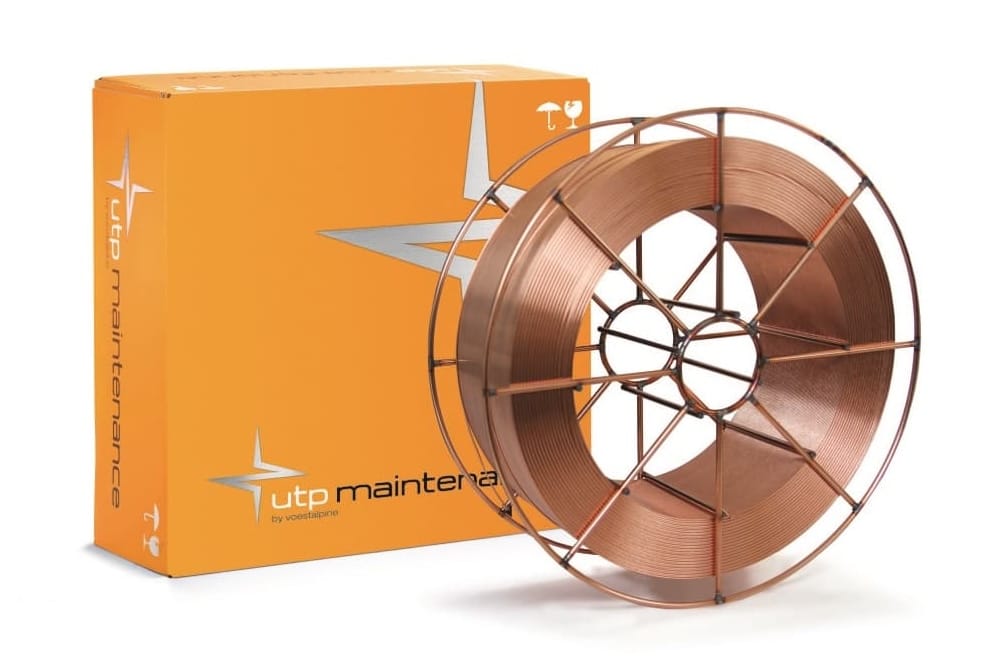
In the world of welding, safety has always been a constant conversation—and it seems like UTP ROBOTIC has taken this to heart with their new seamless, metal-cored wire: the UTP ROBOTIC CHROMELESS 600. This product stands out by cutting out something we all could do without—Hexavalent Chromium (Cr VI). Yes, it’s a hardfacing wire that comes with a serious commitment to reducing health risks, not just for welders but for everyone in the vicinity.
UTP ROBOTIC CHROMELESS 600 is specifically designed to tackle those gritty wear-prone parts, whether it's pressure, impact, or abrasion that’s putting them to the test. What's most notable here is that they've removed both chromium and nickel from the wire’s formula, making it a more health-conscious option without compromising on performance. You still get the abrasion resistance you need—in fact, this wire claims four times less wear loss compared to typical 600 HB flux cored wires—but without the harmful side effects of toxic welding fumes. It’s a win-win for both safety and efficiency.
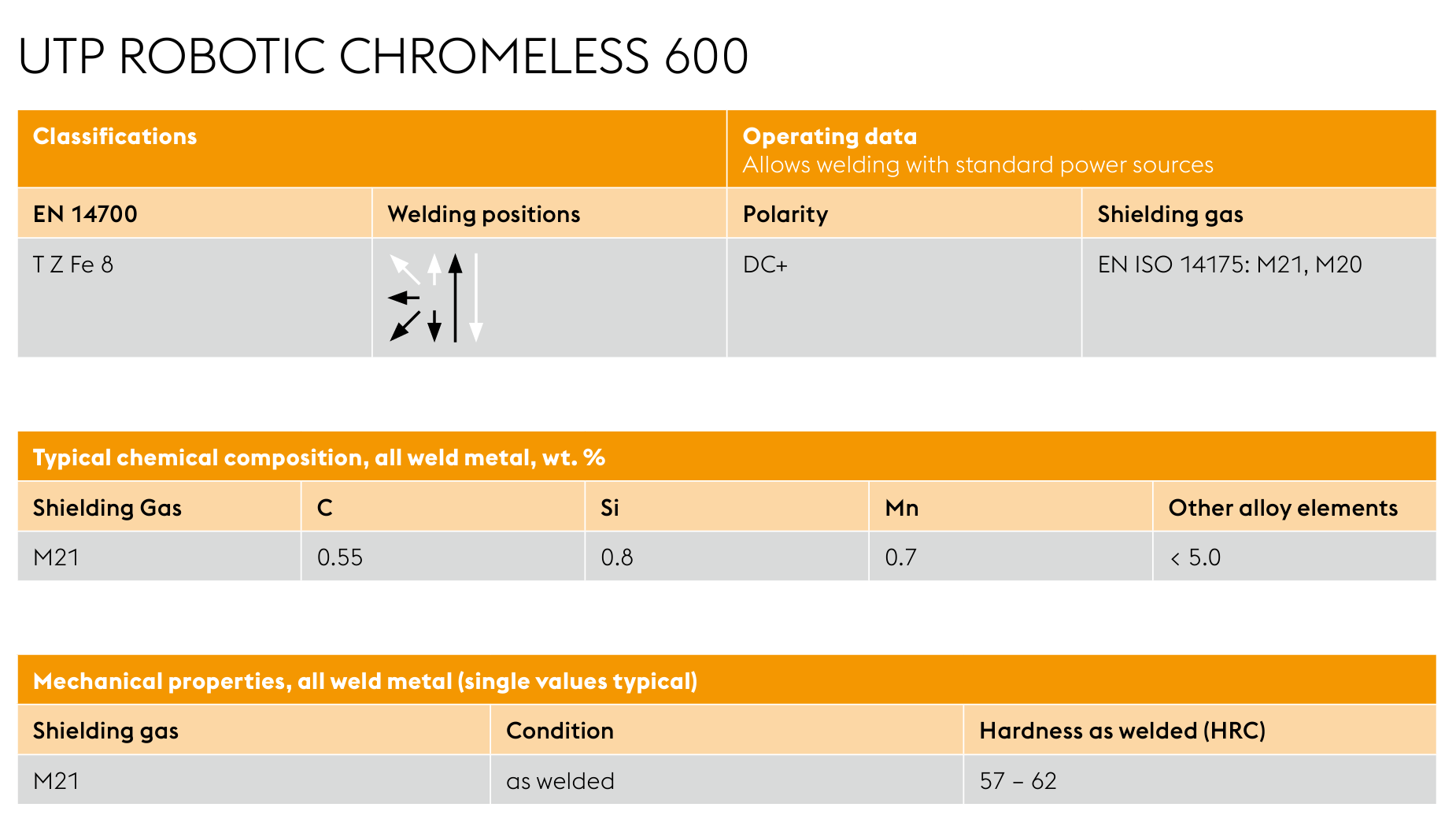
This development also aligns nicely with the tightening regulations in Europe around Occupational Exposure Limits. By going chromeless, UTP ROBOTIC is setting a new standard for workplace safety, showing that it’s possible to protect people without sacrificing quality. So, while Cr VI might be irreplaceable in many high-performance contexts, the UTP ROBOTIC CHROMELESS 600 makes a compelling argument for switching things up where the demands allow—and for doing so safely, without losing sight of performance or longevity. It’s an interesting leap forward for an industry often faced with tough compromises between health and hardness.
For more detail please visit company's page:
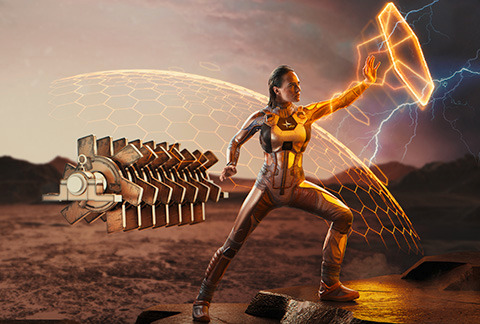
Discussion