New Welding Technique Revolutionizes Wind Turbine Maintenance
I get really excited about these kinds of innovative, multi-partner projects. New welding method developed for wind turbine cast iron components offers a promising solution to reduce waste, cost, and CO2 emissions.
The WeldCast innovation project has delivered something quite promising for the wind energy sector: a new welding technique that aims to repair and assemble large cast iron components in wind turbines. This new method, which emerged from a collaboration involving big players like Siemens Gamesa, Vestas, FORCE Technology, DTU, and Baettr, seeks to tackle the ongoing challenges of maintaining and repairing these massive structures—ultimately aiming to cut down time, costs, and the carbon footprint of wind energy production.
Challenge: The large cast iron elements in wind turbines are expensive and often impossible to repair if defects occur during casting or machining. If the elements can instead be repaired by welding, both time and cost are reduced, and the climate footprint is significantly reduced. Some casters believe that wind turbines are gradually becoming so large that they are difficult to cast, and only a few foundries can perform the task. If a large workpiece can be cast in several pieces and later joined by welding, costs are saved, and the supplier base is expanded considerably.
When it comes to repairing cast iron components, the wind industry faces a particularly stubborn problem. Casting defects in large turbine parts often lead to hefty costs, and many parts end up being scrapped due to the difficulty of repairing them. As turbines continue to increase in size, foundries struggle to keep up with growing demand, making welding repairs a crucial alternative. Thanks to the support of Innovation Fund Denmark and coordination by Energy Cluster Denmark, this project developed a welding technique that might just keep those valuable components in action rather than in the scrap pile.
Has anyone here never watched giant casting technology videos before?
One of the standout features of this innovation is the buttering layer—a novel approach that adapts to the weld and fills defects with another material, reducing the risk of cracks.
"We've developed a buttering layer that adapts to changes in the weld and fills it with another material, allowing us to create welds without cracks or defects," explains Kaare Jensen, Senior Welding Technician at FORCE Technology.
This kind of adaptability could make it easier to repair larger cast iron components without stopping production, providing an alternative to scrapping. As Kaare Jensen from FORCE Technology explains, the practical benefits could be significant, allowing companies to conduct repairs directly on the production line and save both time and resources.
While there's still work to be done before this method can be rolled out commercially, the results are promising. According to Vestas' Anders Vedel, if the implementation happens in the next few years, this welding method could make a real difference for the entire wind energy industry, bringing benefits to both manufacturers and suppliers. If the technology meets its potential, we might see a significant shift in how wind turbines are maintained—making green energy production that much more efficient.
Feel free to check out the WeldCast project details if you're interested.
Source:
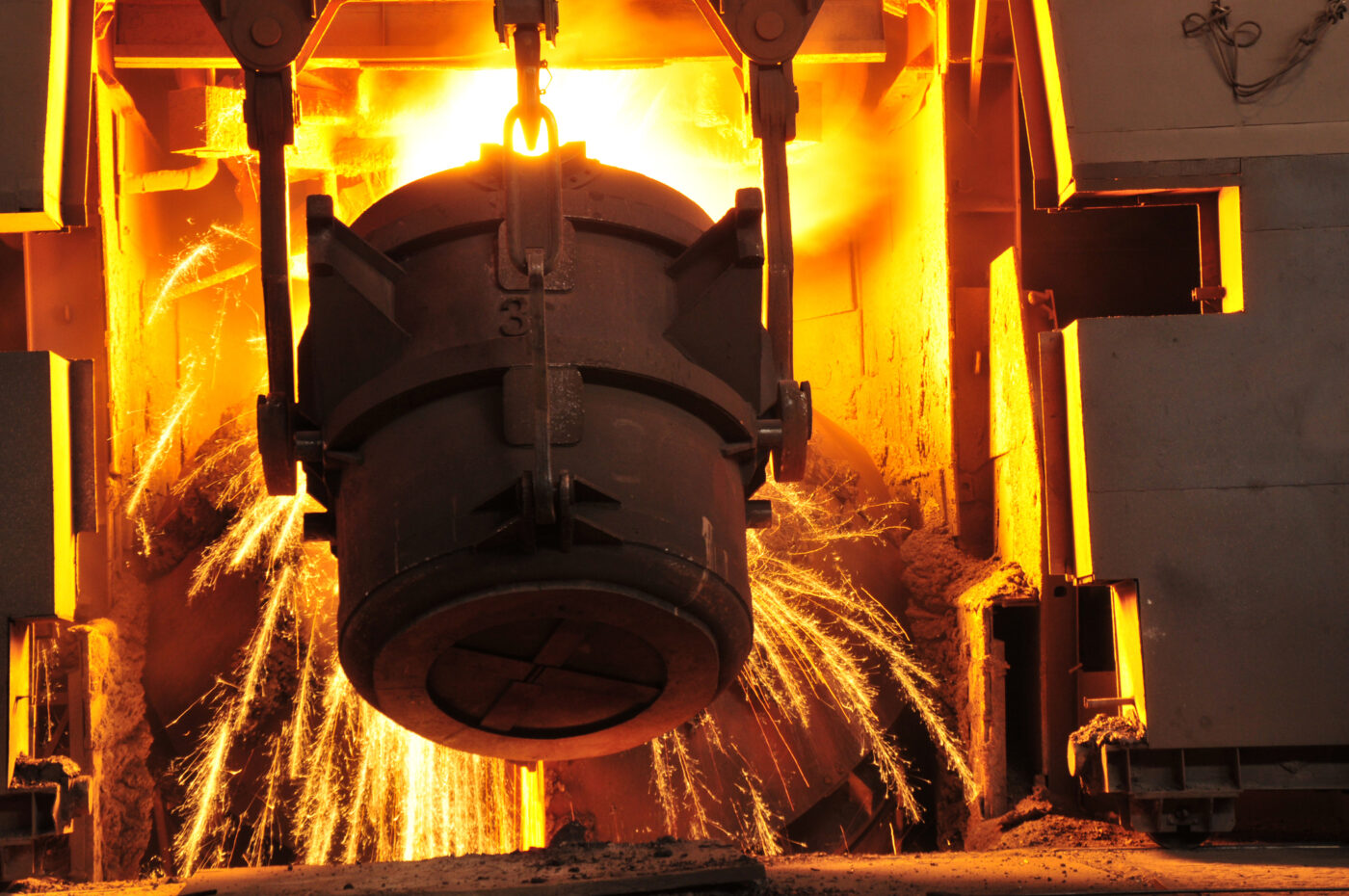
Discussion