Ledbury Welding Ships Modular Fuel Facility to Falklands
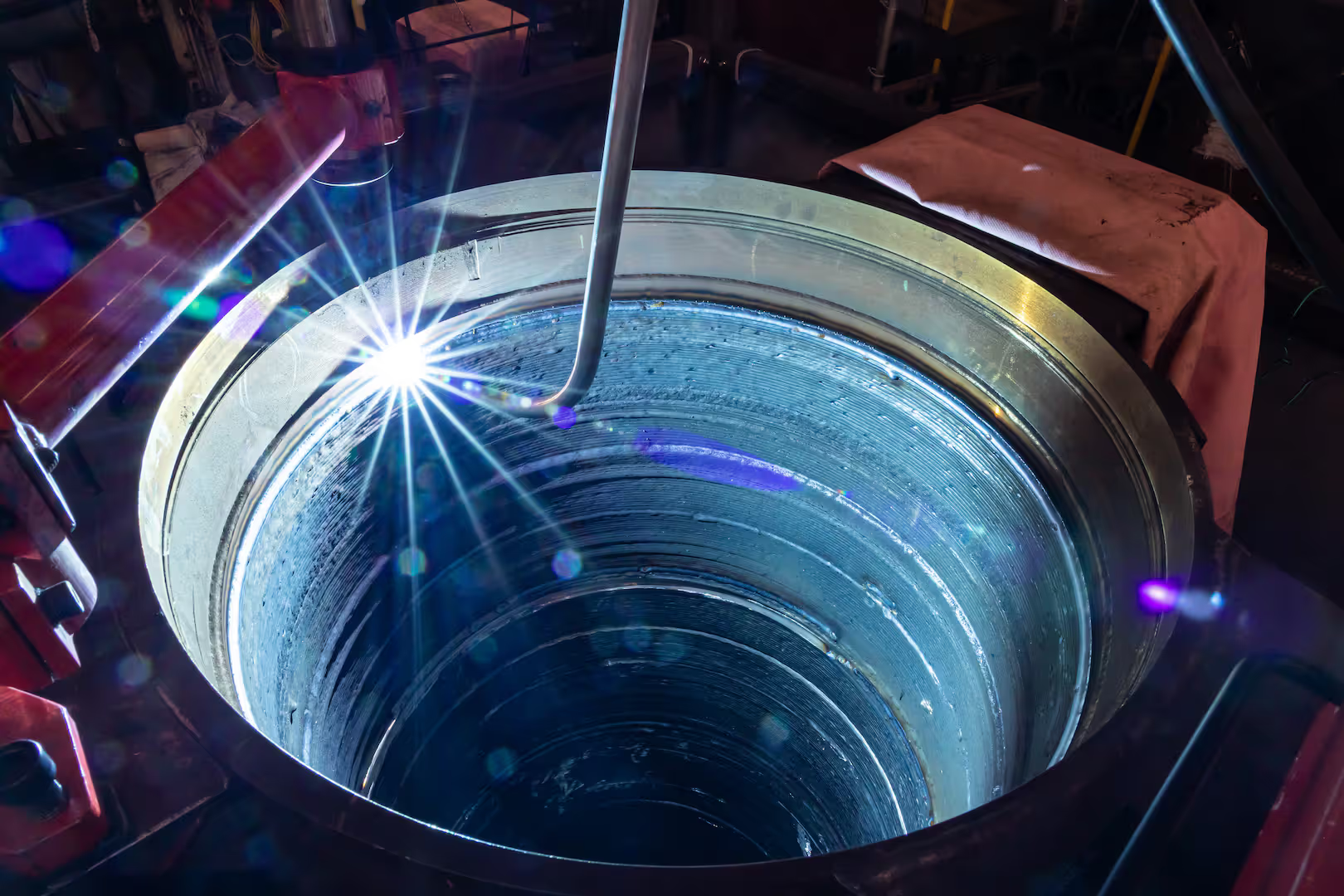
Ledbury Welding & Engineering has completed a fully modular refuelling facility for Stanley Services, bringing British welding know-how to one of the most remote outposts in the South Atlantic. Designed, fabricated and factory-tested in Herefordshire, the unit ships as a single containerised package—proof that a rural UK shop can tackle critical infrastructure on a global stage.
At the core of the system is a SuperVault MH above-ground fuel tank, certified to UL 2085 and rated for four-hour fire resistance, integral secondary containment and impact protection. Surrounding it is an integrated dispensing suite—pipework, pumps, filtration, metering, controls and remote monitoring—built on a compact, plug-and-play frame. The result: larger fuel capacity, faster installation and lower site risk, all sustained by precision welding and stringent quality checks.
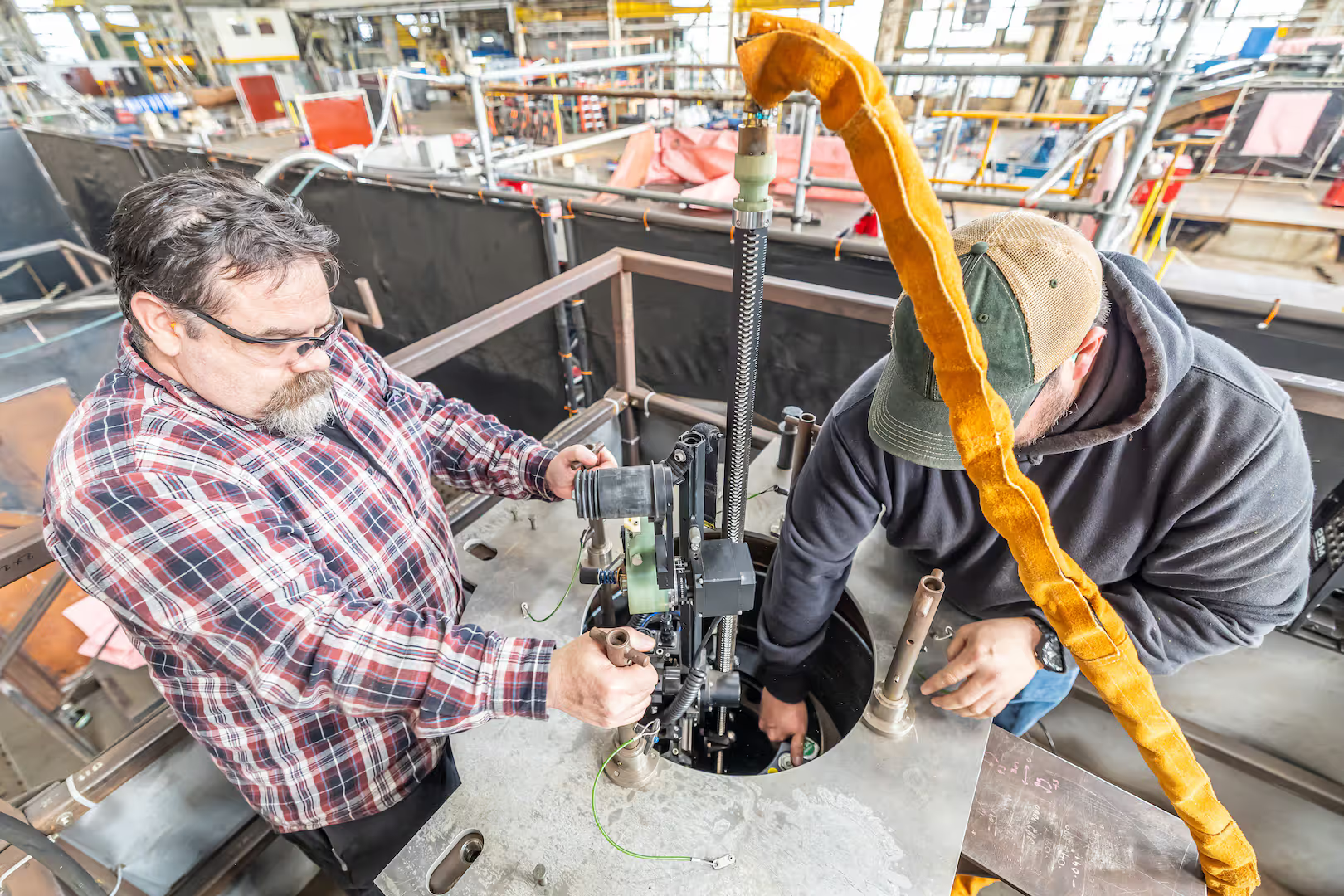
Prefabrication meant every weld, valve and sensor was inspected before the facility left Ledbury’s works, reducing Falklands installation time to days rather than weeks. As energy logistics grow more complex, the project highlights how modular, weld-intensive builds can answer harsh-environment demands—reinforcing Ledbury’s five-decade reputation for reliable fuel systems far beyond the fields of Herefordshire.
Discussion