Facing Challenges in U.S. Shipbuilding: The Role of Welding
I would like to tell you about an article I read on FAB Shop Magazine Direct which highlights the decline of shipbuilding in the United States and the difficulties in regaining its former strength.
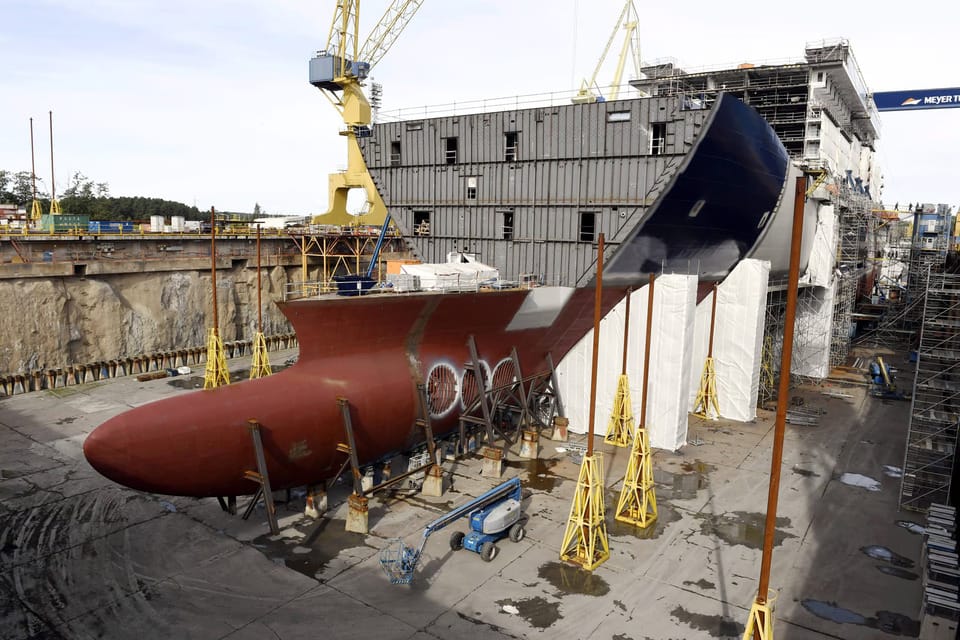
The U.S. shipbuilding industry faces a dual challenge: meeting the rising demand for ships while overcoming a decades-long decline in production capacity. Welding, a backbone of ship construction, plays a pivotal role in this effort. But tight spaces, diverse materials, and a skilled labor shortage make this task complex, requiring innovative solutions to bridge the gap.
“About 40 or 50 years ago, we produced about 5 percent of the world’s ships, but now we only produce about 0.2 percent. Our shipbuilding capacity has dwindled over the years, and that puts a lot of stress on existing shipbuilders to increase productivity. A sizable shipyard has about 4,000 to 5,000 employees, and to keep those people working and possibly add more, we need ships to build. To be competitive in the global market, we must be able to meet the demands of today’s shipyards.” says Rex Hardman
Welding in shipyards is a mix of traditional methods like stick welding, used in confined spaces, and advanced wire feeding processes like flux-cored arc welding (FCAW). Exotic metals like Inconel and stainless steel demand gas tungsten arc welding (GTAW), requiring specialized skills and precision. However, the variability in shipbuilding components limits robotic flexibility, underscoring the ongoing need for skilled welders who can adapt on the fly.
Safety is another pressing concern. From managing welding fumes in confined spaces to dealing with extreme temperatures, shipyards should be sure to supply advanced fume extraction systems and protective equipment. Innovations such as lighter powered air purifying respirators (PAPRs) and low-fume filler metals aim to improve conditions without sacrificing productivity. (Let's be honest. How many shipyards do you think are actually using these devices?)
Now I want to remind you that it was precisely because of the difficult struggles in this field that a Hyundai Samho shipyard was thinking about completely handing over the work to robots. 👇
As shipyards invest in modernizing equipment and incorporating automation, the industry is also working to streamline training for the next generation of welders. With government support, including grants and revitalization plans, the U.S. aims to reclaim its foothold in global ship production—one weld at a time.
Source:
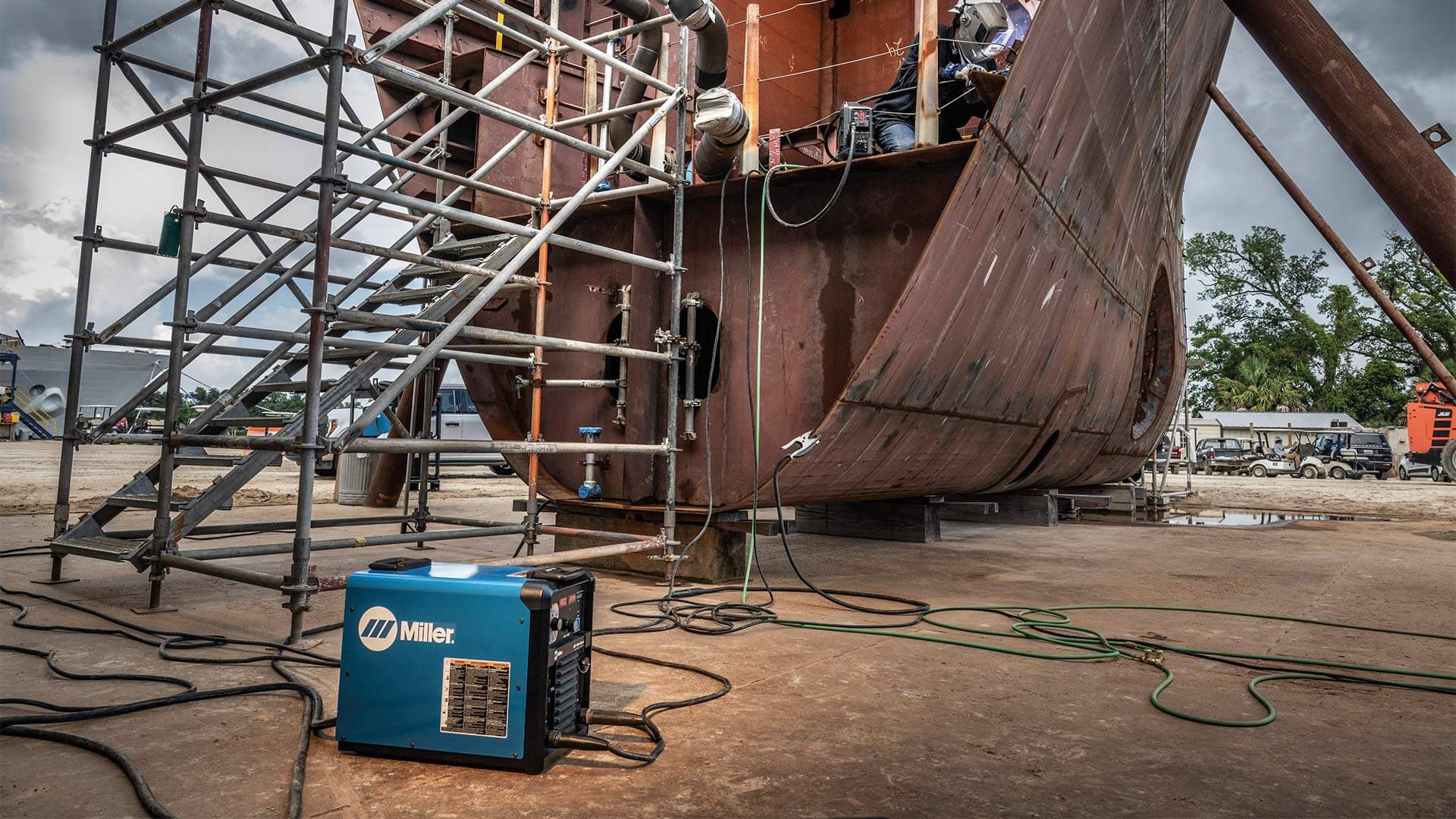
Discussion