Can Pressure Vessels Be Produced With WAAM?
It is now clear that parts with complex geometries can be produced much more efficiently than traditional manufacturing methods.
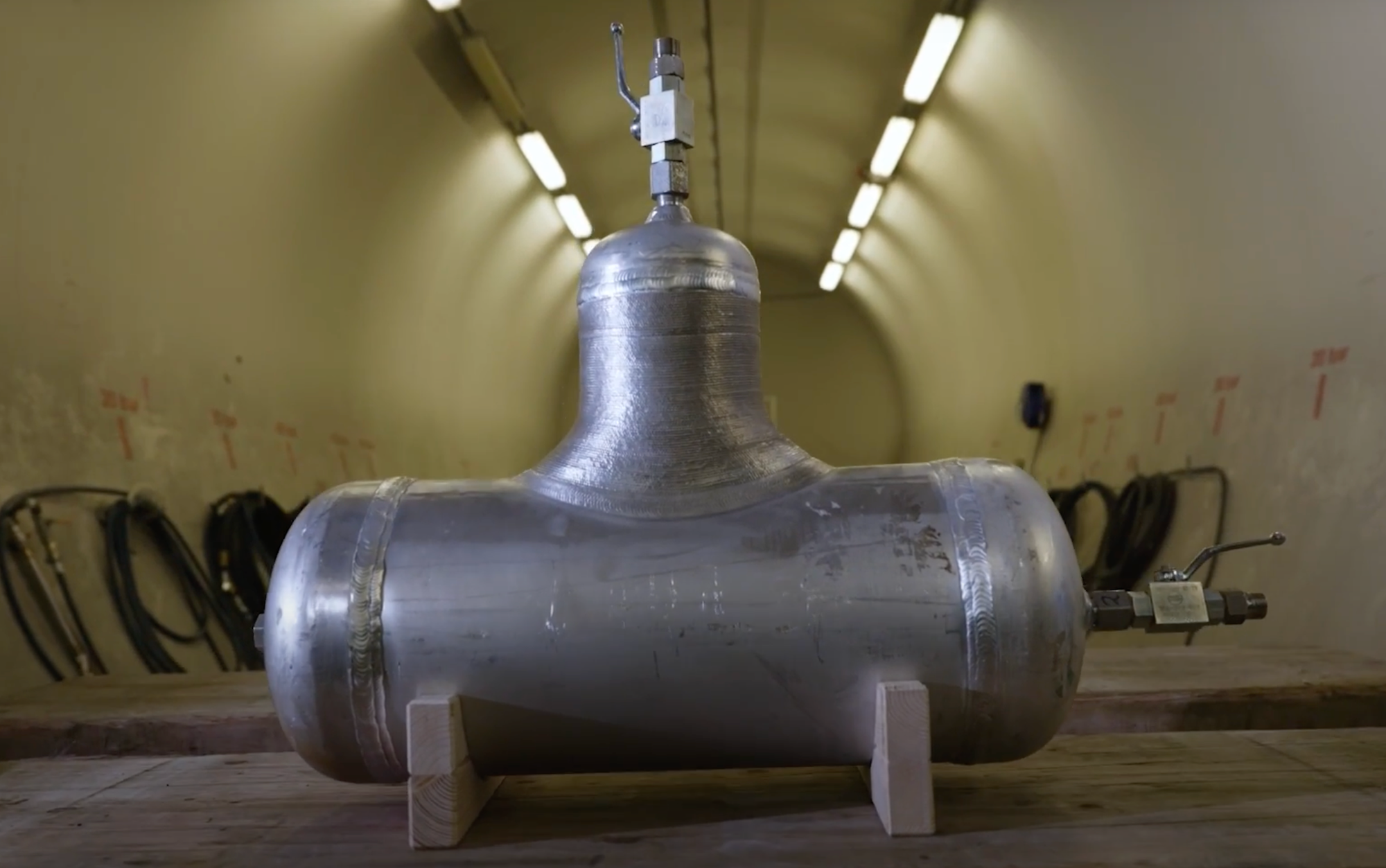
I would like to talk about the article “Metal 3D printing: The future of additive manufacturing” that Fronius published on its blog in September.
The article starts by pointing out how the WAAM method has been making its way into the industry at an increasing pace, especially in the last few years.
It is now clear that parts with complex geometries can be produced much more efficiently than traditional manufacturing methods.
For those who remember, I often try to give space to these topics in my blog, and I have even reported on the latest developments in laser 3D printing.
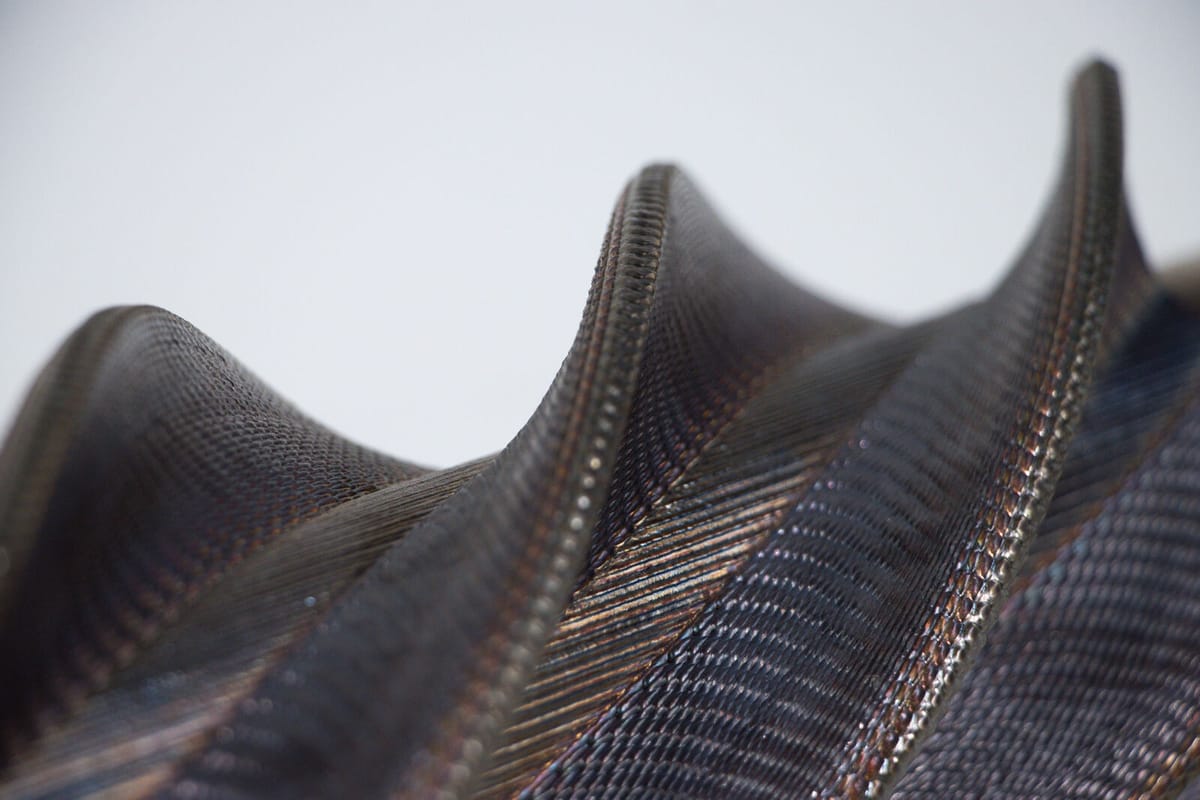
Fronius opens a chapter on WAAM in additive manufacturing processes and underlines the importance of the stable arc required for the process through their patented technology CMT (Cold Metal Transfer).
The part of the article that excites us is the manufacture of a pressure container produced with a special project.
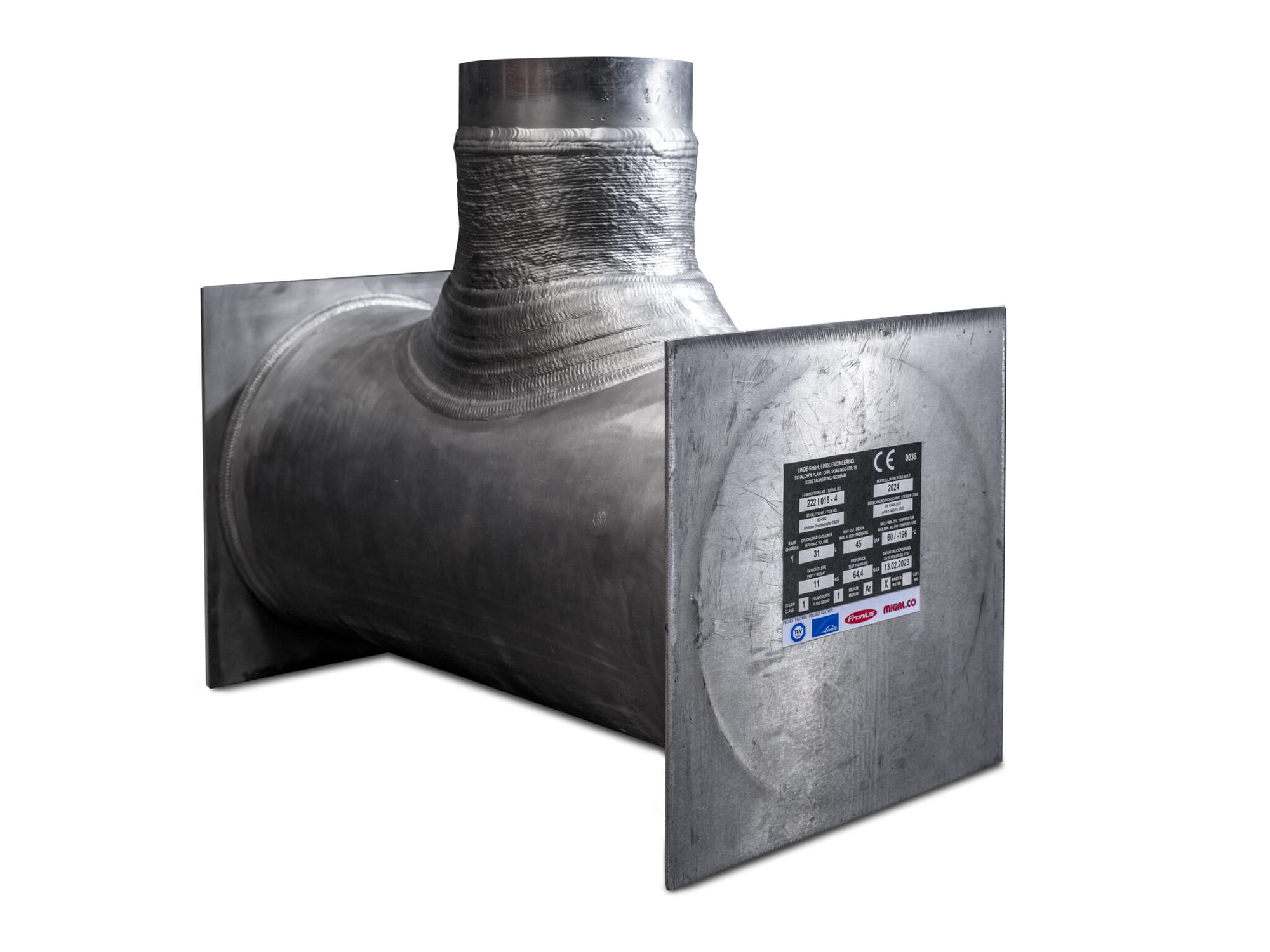
Fronius collaborated with Linde Engineering, Migal.co and TÜV Süd Germany to evaluate the use of draft standard preEN 13445-14 for additively manufactured pressure vessels. The project focused on the model qualification of a pipe branch using a naturally hardened aluminum alloy known for its durability at extremely low temperatures (-273°C).The entire process from design to final pressure testing was reviewed and documented. The draft standard covers the entire value chain of additive manufacturing, ensuring that all safety requirements set out in the Pressure Equipment Directive are met.
I strongly recommend that those interested in the subject watch the video as well. (English subtitles are also available)
You can access the full article from the link. 👇
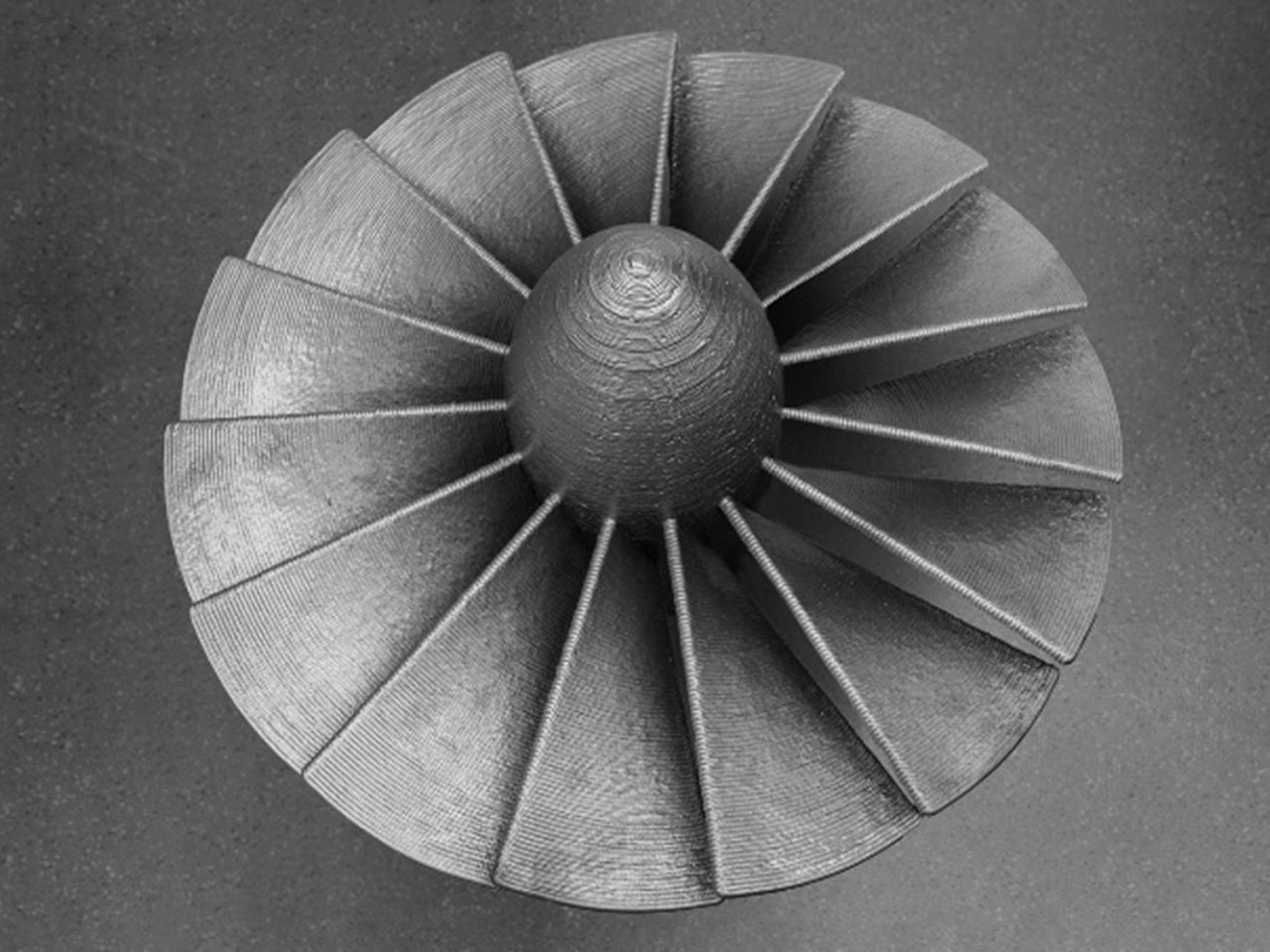

Discussion