Al-Cu Hybrids Could Lighten Future EVs
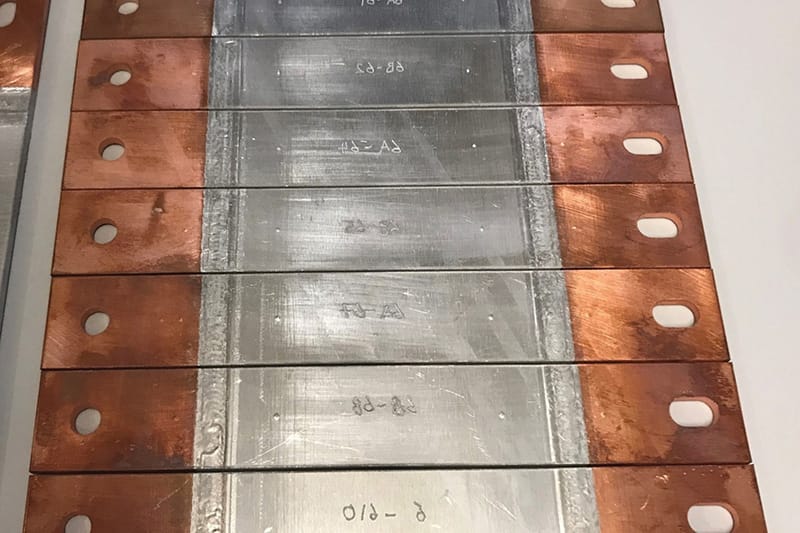
Researchers at the Norwegian University of Science and Technology (NTNU) are developing a welding method to produce aluminium-copper hybrid conductors aimed at reducing the weight of electric vehicles (EVs). Using a process called Hybrid Metal Extrusion and Bonding (HYB), which resembles friction stir welding, the team successfully joined aluminium and copper without creating thick, brittle intermetallic layers that normally reduce conductivity.
The HYB process uses a rotating pin to extrude an aluminium filler metal rich in silicon and magnesium while simultaneously bonding it with copper. This controlled deformation and localized heat input allows the metals to bond at the atomic level without compromising their mechanical or electrical performance. The resulting conductors, made from roughly 50:50 aluminium and copper, could reduce wiring weight by up to 35%, with possible further savings through optimized alloy design.
Though more research is needed to improve the mechanical strength of the aluminium side, especially under heat, the potential industrial impact is significant. Lighter wiring can trim 1–3% of an EV’s total weight and bring notable cost advantages. NTNU and SINTEF are now collaborating to refine the process and explore how alloying elements like magnesium and silicon affect performance at the weld interface.
Source:
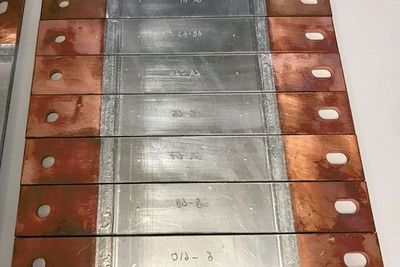
Discussion