Advancing Ammonia Tank Welding with New Wire Technology
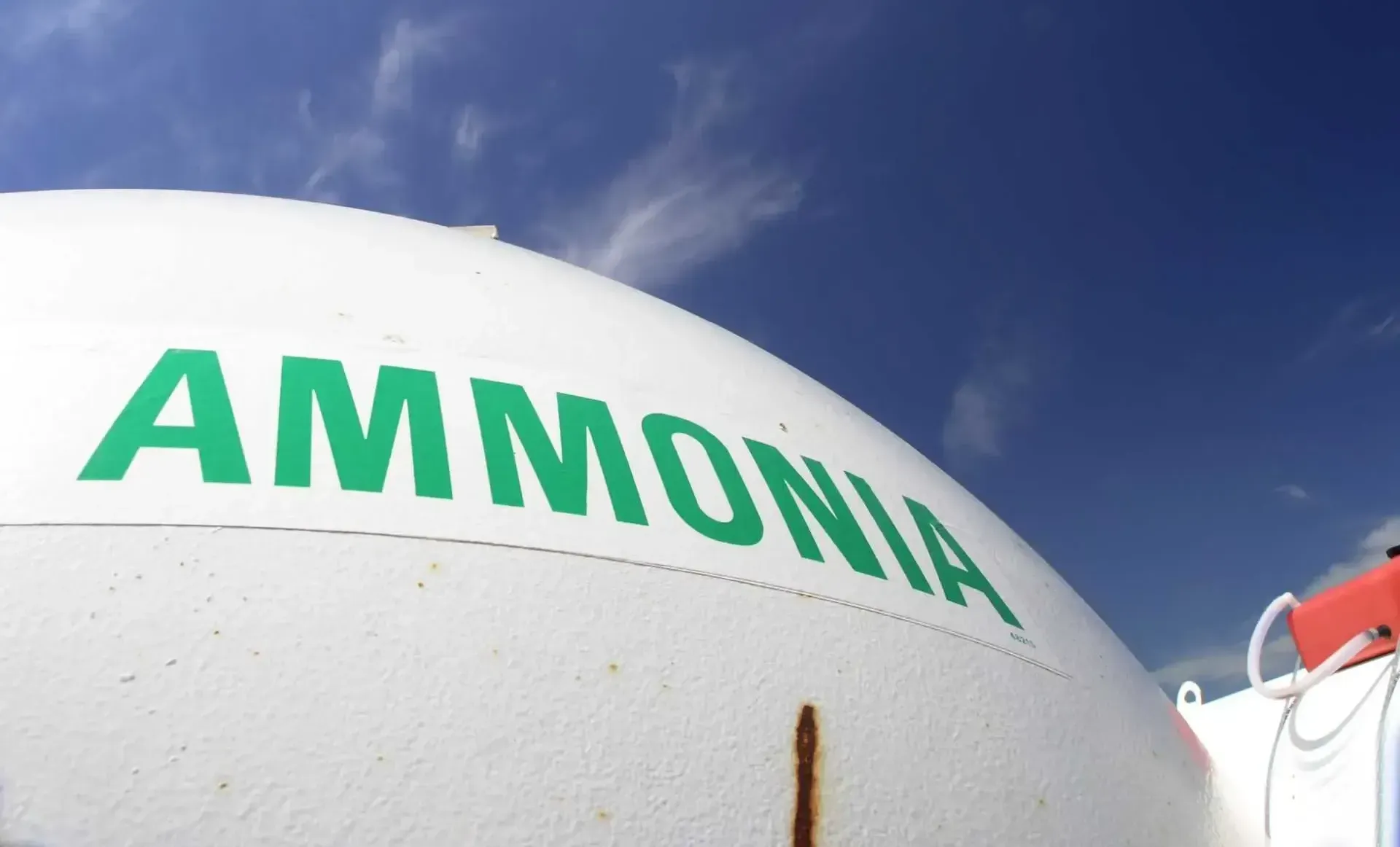
Linde Engineering and voestalpine Böhler Welding have successfully developed a specialized welding wire solution to improve ammonia tank construction. As ammonia gains importance in the clean energy transition, storage tanks must be built with materials and welding techniques that withstand stress corrosion cracking (SCC). The collaboration between the two companies aims to enhance welding efficiency, addressing industry demands for larger storage capacities and tighter project timelines.
The solution integrates voestalpine Böhler Welding’s diamondspark seamless wire technology, which offers superior mechanical properties for ammonia tank welding. When used with the railRunner system, a mechanized welding carriage, the process allows for fully automated root pass, fill, and cap layer welding. This innovation increases productivity compared to manual stick electrode welding, reduces welding consumables, and simplifies integration into daily welding operations.
Welding trials for this new approach have been conducted in India, with qualification tests ongoing at the Böhler Application Technology Center. The project highlights the role of automation and advanced welding materials in optimizing large-scale industrial construction. On-site support from voestalpine Böhler Welding ensures proper setup and parameter adjustments, further maximizing efficiency in ammonia tank fabrication.
This collaboration reflects a shared commitment to innovation in welding. By combining Linde’s expertise in ammonia-specific materials with Böhler Welding’s consumables and automation technology, the industry now has a more efficient, scalable, and high-quality solution for ammonia storage construction.
Source:
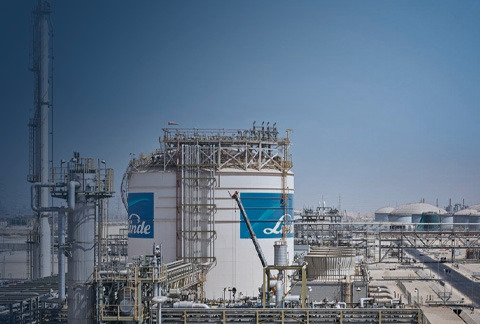
Discussion